6×7-IWS鍍鋅鋼絲繩的彎曲疲勞性能測(cè)試
作者: admin 編輯: admin 來(lái)源:admin 發(fā)布日期:2020-03-14 14:13
信息摘要:
0引言 鋼絲繩具有較高抗拉強(qiáng)度、承載能力、抗沖擊韌性以及柔軟性和吸收阻尼的特點(diǎn)。在海洋工程、橋梁工程、礦山工程以及航空航天事業(yè)中都離不開(kāi)鋼絲繩的應(yīng)用。不僅如此,日常
0引言
鋼絲繩具有較高抗拉強(qiáng)度、承載能力”、抗沖擊韌性“以及柔軟性和吸收阻尼”的特點(diǎn)。在海洋工程、橋梁工程、礦山工程“以及航空航天事業(yè)”中都離不開(kāi)鋼絲繩的應(yīng)用。不僅如此,日常生活中也隨處可見(jiàn)鋼絲繩的應(yīng)用,如升降電梯,自動(dòng)升降衣架。為了防止鋼絲繩使用過(guò)程中突然斷裂而造成的人員生命安全以及財(cái)產(chǎn)損失,研究鋼絲繩的失效過(guò)程以及疲勞壽命也就具有重要的意義。目前,有關(guān)鋼絲繩彎曲疲勞以及微動(dòng)疲勞的研究越來(lái)越多“l,但大多數(shù)均是針對(duì)大規(guī)格、粗規(guī)格的鋼絲繩,研究細(xì)規(guī)格鋼絲繩的學(xué)者很少,王春輝小組“四在研究小直徑鋼絲繩軸向疲勞時(shí)的鋼絲直徑也高達(dá)16mm。而隨著設(shè)備精細(xì)化、輕量化的發(fā)展,鋼絲繩也不再僅限于大規(guī)格、粗規(guī)格的應(yīng)用""。因此,通過(guò)對(duì)6×7-lWS-p1.95mm細(xì)規(guī)格鍍鋅鋼絲繩進(jìn)行彎曲疲勞研究,分析掌握其彎曲失效的基本形式,探索影響鋼絲繩彎曲疲勞的影響因素也就具有重要的意義。
1實(shí)驗(yàn)方法
1.1試驗(yàn)材料
本實(shí)驗(yàn)采用日本進(jìn)口碳含量為0.72%左右的盤條作為原材料先生產(chǎn)出半成品鍍鋅鋼絲,然后再用半成品鍍鋅鋼絲生產(chǎn)出成品鋼絲。成品鋼絲經(jīng)捻股以及合繩工序后得到鋼絲繩樣品。其中盤條化學(xué)成分和半成品鍍鋅鋼絲的各項(xiàng)性能如表1與表2所示。

1.2樣品制備與實(shí)驗(yàn)設(shè)備
對(duì)半成品鍍鋅鋼絲進(jìn)行水箱拉拔,分別獲得直徑為0.21mm、0.23mm、0.24mm、0.25mm四種規(guī)格的鋼絲,然后再經(jīng)過(guò)捻股機(jī)生產(chǎn)出結(jié)構(gòu)為0.23+6×0.21的外繞股以及結(jié)構(gòu)為0.25+6×0.24的中心股,最后經(jīng)合繩機(jī)生產(chǎn)出結(jié)構(gòu)為6×7-IWS的交互捻鍍鋅鋼絲繩,鋼絲繩破斷拉力為5050N。鋼絲繩橫截面結(jié)構(gòu)如圖1所示。
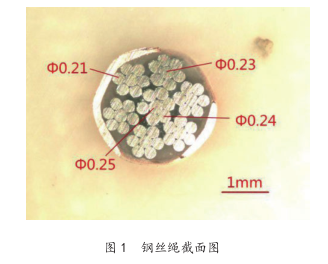
1.3實(shí)驗(yàn)方法與原理
以3000次實(shí)驗(yàn)為起始次數(shù),每隔500次作為一次節(jié)點(diǎn)進(jìn)行實(shí)驗(yàn)記錄,直到鋼絲繩全斷時(shí)停止。每個(gè)節(jié)點(diǎn)次數(shù)安排兩次實(shí)驗(yàn),即每個(gè)次數(shù)節(jié)點(diǎn)有10根樣品。對(duì)不同彎曲次數(shù)下的鋼絲繩樣品進(jìn)行彎曲工作段(約1060mm)的拆股解捻處理,記錄鋼絲繩不同層中鋼絲的斷絲情況,并對(duì)不同層中的斷裂鋼絲進(jìn)行微觀形貌觀察。與多數(shù)學(xué)者的研究方法不同,本文中的疲勞機(jī)有三個(gè)被動(dòng)輥輪,三個(gè)輥輪之間的相對(duì)位置固定。鋼絲繩通過(guò)疲勞機(jī)中固定端的壓板進(jìn)行一端固定,另一端懸掛配重,鋼絲繩中間部分繞過(guò)三個(gè)輥輪,通過(guò)輥輪在導(dǎo)軌上的往復(fù)運(yùn)動(dòng)對(duì)鋼絲繩進(jìn)行彎曲測(cè)試,本實(shí)驗(yàn)機(jī)在業(yè)內(nèi)稱為三輥疲勞機(jī)]。
2實(shí)驗(yàn)結(jié)果與分析
2.1不同層鋼絲的斷絲率統(tǒng)計(jì)
本實(shí)驗(yàn)中,6×7-lWS-p1.95mm鍍鋅鋼絲繩在疲勞機(jī)中的極限彎曲次數(shù)為9500次,通過(guò)記錄3000次至9500次每個(gè)節(jié)點(diǎn)不同鋼絲的斷絲率可得如圖3所示數(shù)據(jù)。從圖3中可知,6×7-lWS-p1.95mm鍍鋅鋼絲繩從彎曲次數(shù)達(dá)到3500次時(shí)開(kāi)始出現(xiàn)斷絲,斷絲的鋼絲為鋼絲繩最外層00.21mm鋼絲。隨著疲勞次數(shù)增加至4500次時(shí),芯股的中心鋼絲④0.25mm與芯股外繞絲40.24mm開(kāi)始出現(xiàn)斷絲。雖然,④0.25mm與①0.24
mm鋼絲比鋼絲繩最外層p0.21mm鋼絲晚出現(xiàn)斷絲,但均比40.21mm鋼絲先達(dá)到100%的斷絲率。值得關(guān)注的是,鋼絲繩外繞股的中心鋼絲(④0.23mm僅在鋼絲繩接近極限狀態(tài)時(shí),才開(kāi)始有斷裂的鋼絲產(chǎn)生,0.23mm鋼絲基本都是隨著整繩斷裂而斷裂。根據(jù)實(shí)驗(yàn)推斷,
6×7-IWS結(jié)構(gòu)鋼絲繩中外繞股的中心鋼絲在鋼絲繩彎曲測(cè)試過(guò)程中具有重要的作用。
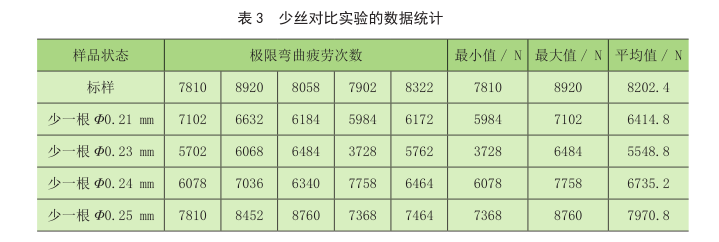
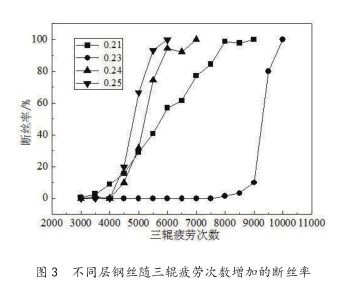
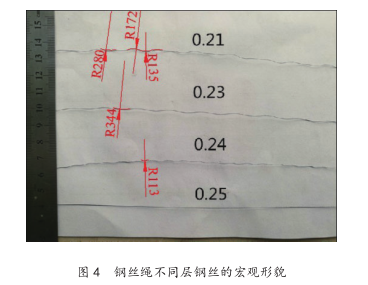
為了進(jìn)一步研究鋼絲繩中不同層鋼絲對(duì)鋼絲繩彎曲疲勞性能的影響,安排了同種結(jié)構(gòu)鋼絲繩的缺絲對(duì)比實(shí)驗(yàn),實(shí)驗(yàn)數(shù)據(jù)如表3中所示。從表3中數(shù)據(jù)可明顯看出,在缺少一根④0.23mm單絲時(shí),鋼絲繩的極限疲勞次數(shù)下降的幅度最大,由此可見(jiàn),與鋼絲繩中其它位置的鋼絲相比,外套股中心鋼絲的有無(wú)對(duì)鋼絲繩整體的彎曲疲勞壽命影響最大。
2.2不同層鋼絲的結(jié)構(gòu)分析
圖4是6×7-IWS-1.95mm鍍鋅鋼絲繩拆股解捻后不同層鋼絲的宏觀形貌,從圖中可以看出,作為鋼絲繩芯股的中心絲,60.25mm鋼絲沒(méi)有任何波形結(jié)構(gòu);b0.23mm與60.24mm鋼絲均表現(xiàn)出單一的波形結(jié)構(gòu);而50.21mm鋼絲具有復(fù)合波形結(jié)構(gòu)。結(jié)合鋼絲繩捻制工藝可知,各鋼絲中波形的波高與波長(zhǎng)尺寸與鋼絲繩的捻制參數(shù)有關(guān),即50.23mm鋼絲的波形波長(zhǎng)與鋼絲繩的繩捻距有關(guān),波高與鋼絲繩的粗度和外繞股的粗度有關(guān);50.24mm鋼絲的波形波長(zhǎng)與波高分別與芯股的捻距和粗度有關(guān);而具有復(fù)合波形的50.21mm鋼絲的波形既和繩捻距、粗度有關(guān),也與外繞股的捻距、粗度有關(guān)。通過(guò)對(duì)不同鋼絲中波形的曲率半徑進(jìn)行測(cè)量可得,
50.21mm鋼絲中存在三種曲率半徑的波形,分別為R280、R172、R135;0.23mm鋼絲中只存在曲率半徑為R344的波形;0.24mm鋼絲中也只存在一種曲率半徑為R1l3的波形。
分析認(rèn)為:鋼絲繩彎曲疲勞測(cè)試過(guò)程中,具有不同波形結(jié)構(gòu)的鋼絲在鋼絲繩中的受力也各不相同。50.23
mm的鋼絲在鋼絲繩彎曲測(cè)試過(guò)程中,波形曲率半徑大,由于鋼絲結(jié)構(gòu)的原因,鋼絲在軸向具有一定的結(jié)構(gòu)彈性,在鋼絲繩彎曲疲勞過(guò)程中抵抗斷裂的性能好。具有復(fù)合波形結(jié)構(gòu)的50.21mm鋼絲,由于具有多種波形,鋼絲上的應(yīng)力分布復(fù)雜。0.24mm鋼絲的波形雖然不是復(fù)合波形,但整體波形尺寸小,波形曲率半徑最小,鋼絲繩彎曲疲勞過(guò)程中在波峰與波谷處產(chǎn)生的應(yīng)力比0.23
mm和(50.21mm的都大。0.25mm鋼絲雖然不具有波形,但作為鋼絲繩繩芯的組成單元,在鋼絲繩受軸向拉應(yīng)力時(shí),繩芯鋼絲產(chǎn)生的應(yīng)力最大,使得繩芯處鋼絲的疲勞壽命值低:其次,相同規(guī)格的簾線成品,鋼絲的絲徑越祖,其抗疲勞性能越差",使得(0.25mm中心鋼絲在鋼絲繩彎曲疲勞過(guò)程中斷裂速度過(guò)快。
2.3鋼絲表面形貌與斷口觀察圖5是鋼絲繩最外層鋼絲的表面形貌圖。從圖5a圖可以看出經(jīng)過(guò)彎曲測(cè)試后鋼絲繩最外層鋼絲(40.21
mm)表面沿軸向存在橢圓狀的磨損傷疤(圖中A處),與微動(dòng)磨損產(chǎn)生的磨損形貌類似四。結(jié)合彎曲疲勞機(jī)的工作原理可知,此損傷主要是由鋼絲繩外層鋼絲與三輥疲勞機(jī)輥輪的相互摩擦所致。從圖5b圖可以看出外層股與外層股中鋼絲之間的相互擠壓摩擦同樣使鋼絲表面產(chǎn)生了磨損傷疤。相鄰股接觸表面存在嚴(yán)重的擠壓磨痕,不僅使單絲截面變形較大,而且也容易在早期形成裂紋的萌生。
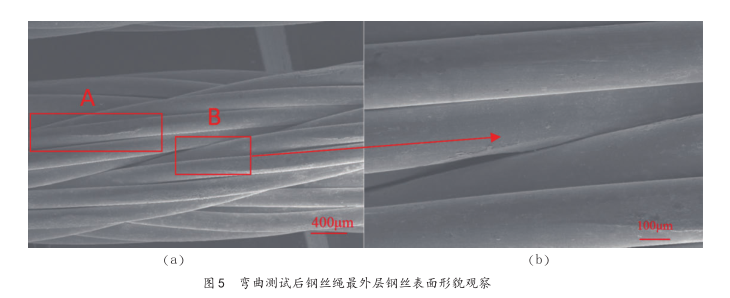
如圖6是鋼絲繩內(nèi)芯股表面鋼絲的損傷觀察,從圖中可觀察到芯股表面鋼絲(50.24mm)存在明顯的磨損傷疤,且磨損傷疤的邊緣還殘留著少許磨屑。根據(jù)鋼絲繩的捻制工藝可知,鋼絲繩內(nèi)外繞股與芯股呈點(diǎn)接觸狀態(tài),即外繞股中50.21mm鋼絲和芯股中的(50.24mm鋼絲兩者在鋼絲繩彎曲疲勞測(cè)試過(guò)程中為點(diǎn)接觸狀態(tài)。隨著彎曲疲勞次數(shù)的增加,接觸點(diǎn)處鋼絲逐漸磨損,沿軸向形成橢圓狀的磨損傷疤,與倪響國(guó)在研究表面損傷對(duì)鋼絲繩彎曲疲勞性能時(shí)觀察到的股與股之間鋼絲微動(dòng)磨損形貌一致。M,Torkar,B.Areznsek等人也認(rèn)為交互輪鋼絲繩在使用時(shí),金屬繩芯中鋼絲與外繞股鋼絲存在點(diǎn)接觸微動(dòng)磨損,并引起芯股的嚴(yán)重?cái)嘟z。截止目前,經(jīng)過(guò)彎曲疲勞測(cè)試后的鋼絲繩中主要存在上述磨損缺陷,暫未發(fā)現(xiàn)其他類型的磨損形貌或腐蝕現(xiàn)象。
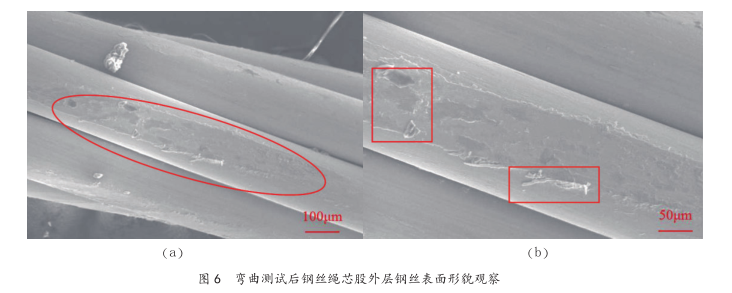
如圖7是不同層鋼絲斷口的電子掃描照片,其中0.23mm樣品來(lái)自疲勞次數(shù)為8000次時(shí),出現(xiàn)的唯一一根斷裂的60.23mm鋼絲。通過(guò)斷口形貌的觀察可知,這四種鋼絲均屬于疲勞斷裂,例如圖7b和圖7c中均可以觀察到明顯的疲勞源區(qū)(A區(qū)),疲勞源區(qū)呈現(xiàn)出光滑的平面形貌,這種形貌的產(chǎn)生是因?yàn)榱鸭y在疲勞源處產(chǎn)生后隨著鋼絲后續(xù)不斷的彎折,使得裂紋部位不斷的張開(kāi)與閉合,疲勞源處逐漸被磨平,從而形成疲勞源區(qū)這種特殊的斷口形貌。裂紋從疲勞源區(qū)誕生后會(huì)逐漸的向鋼絲中心部位擴(kuò)展形成裂紋擴(kuò)展區(qū)(B區(qū)),并裂紋擴(kuò)展過(guò)程中形成較多的二次裂紋。在裂紋擴(kuò)展區(qū)之后,鋼絲在存在較大的軸向載荷的情況下便會(huì)發(fā)生瞬時(shí)斷裂形成瞬斷區(qū),并且瞬斷區(qū)會(huì)在鋼絲瞬時(shí)斷裂時(shí)與鋼絲橫截面成較大的傾斜角度(C區(qū))。圖7b和圖c就是典型的鋼絲疲勞斷口,與倪響在對(duì)6×19點(diǎn)接觸鋼絲繩彎曲疲勞實(shí)驗(yàn)中所觀察的結(jié)果一致。而圖7a與圖7d僅能夠觀察到疲勞斷裂的部分特征,如裂紋源區(qū)。引起疲勞源區(qū)的因素有很多,主要有鋼絲材質(zhì)以及表面本身的缺陷、鋼絲表面的摩擦磨損、鋼絲表面的腐蝕。結(jié)合圖5與圖6中鋼絲表面的形貌分析,本文中各規(guī)格鋼絲疲勞源產(chǎn)生的主要原因應(yīng)是鋼絲表面的摩擦磨損,如圖7a中的0.21mm鋼絲橫截面已不再是圓形,它反映的是具有橢圓狀磨損傷疤處鋼絲截面的形貌。
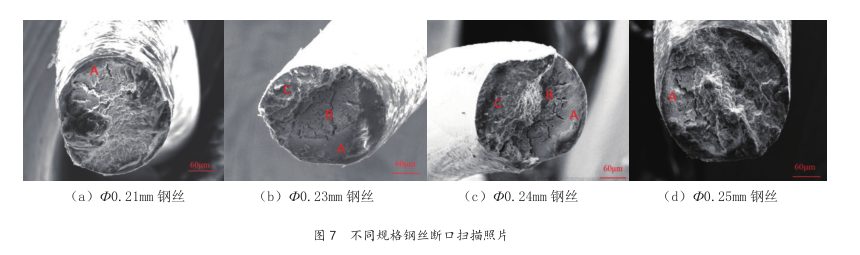
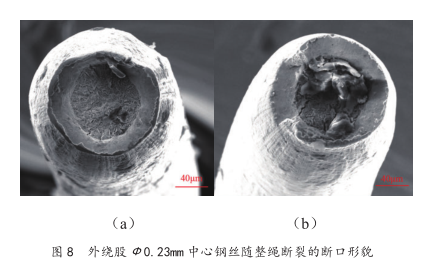
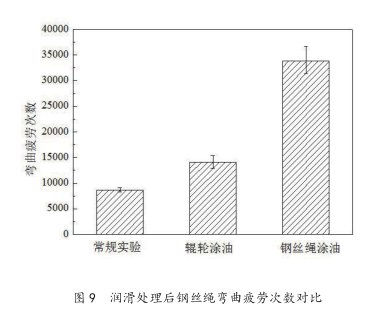
如圖8是外繞股40.23mm中心鋼絲隨整繩斷裂后的斷口形貌,從圖中可以看出④0.23mm鋼絲斷口中存在明顯的頸縮現(xiàn)象,鋼絲被拉斷。但是與常規(guī)的鋼絲頸縮斷口形貌相比,又有著不同之處。40.23mm鋼絲斷口中芯部有明顯的二次裂紋,而常規(guī)鋼絲頸縮斷口芯部會(huì)形成細(xì)小的韌窩。分析認(rèn)為,0.23mm鋼絲在鋼絲繩彎曲疲勞過(guò)程中形成了疲勞損傷,從而使鋼絲在較大載荷的情況下,形成芯部具有二次裂紋而不是韌窩的頸縮形貌。
為了研究摩擦磨損對(duì)鋼絲繩彎曲過(guò)程中影響因素的大小,安排了涂油潤(rùn)滑后的鋼絲繩彎曲疲勞實(shí)驗(yàn)。圖9是涂油潤(rùn)滑后鋼絲繩彎曲疲勞次數(shù)的對(duì)比圖,結(jié)果表明,僅對(duì)疲勞機(jī)輥輪的輪槽內(nèi)表面進(jìn)行潤(rùn)滑處理時(shí),鋼絲繩的極限彎曲疲勞次數(shù)提升至原來(lái)的1.5倍左右;而直接對(duì)鋼絲繩彎曲工作段進(jìn)行全面潤(rùn)滑處理時(shí),鋼絲繩的極限彎曲疲勞次數(shù)提升至原來(lái)的4倍左右。
根據(jù)實(shí)驗(yàn)推斷,直接在鋼絲繩中涂油的潤(rùn)滑效果要比僅在疲勞機(jī)輥輪上涂油的潤(rùn)滑效果好,因?yàn)閷?duì)鋼絲繩直接涂油時(shí),鋼絲繩內(nèi)部也會(huì)由于潤(rùn)滑油的浸入而得到潤(rùn)滑:而在輥輪上涂油,滾輪上潤(rùn)滑油量有限,僅僅能改善鋼絲繩表層鋼絲與輥輪間的潤(rùn)滑狀態(tài)。但不管改善鋼絲繩與輥輪間的潤(rùn)滑狀況,還是改善鋼絲繩內(nèi)部鋼絲與鋼絲的潤(rùn)滑狀況均可以在較大程度上推遲裂紋產(chǎn)生的時(shí)間,提高鋼絲繩的彎曲疲勞壽命。
3結(jié)論
通過(guò)對(duì)結(jié)構(gòu)為6×7-IWS-01.95mm的鋼絲繩進(jìn)行彎曲疲勞測(cè)試可知:
1)6×7-IWS結(jié)構(gòu)鋼絲繩外繞股中心鋼絲對(duì)鋼絲繩的彎曲疲勞壽命具有非常重要的影響,外繞股中心鋼絲所具有的相對(duì)較大且單一的波形結(jié)構(gòu),是其在鋼絲繩彎曲疲勞過(guò)程中抵抗斷裂的主要原因;
2)鋼絲繩中鋼絲的彎曲測(cè)試斷口均為疲勞斷口,疲勞源產(chǎn)生的主要原因是鋼絲表面的摩擦磨損,改善鋼絲繩工作時(shí)與輥輪間的潤(rùn)滑狀態(tài)以及鋼絲繩內(nèi)部鋼絲與鋼絲間的潤(rùn)滑狀態(tài)均能在較大程度上提升鋼絲繩的彎曲疲勞壽命。
本網(wǎng)站內(nèi)容由昌源鋼繩小編整理、編輯、發(fā)布。如您轉(zhuǎn)載時(shí),請(qǐng)帶上本文標(biāo)題與鏈接,昌源鋼繩感謝您的支持,我們會(huì)一如既往提供高質(zhì)量鋼絲繩產(chǎn)品與優(yōu)質(zhì)的技術(shù)指導(dǎo)服務(wù),昌源鋼繩感謝有您相伴!
標(biāo)題:6×7-IWS鍍鋅鋼絲繩的彎曲疲勞性能測(cè)試 鏈接:/gangshengbaike/410.html